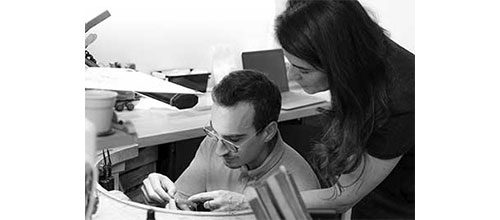
Our Parisian workshop is located in the historic heart of the diamond district and the jewelry workshops of Paris, a stone's throw from Montmartre. It works for the greatest fine jewelry houses on the Place Vendôme, which allows us to offer you pieces of irreproachable quality, with an exceptional quality / price ratio because our costs are very carefully considered.
The diamond dealer and the gem dealer
He travels the world in search of the most beautiful gems, which are offered to jewelry houses. Sometimes he buys rough stones which are then cut to order. For diamonds, very sophisticated software studies the roughs and optimizes their size according to the inclusions present and the shape of the crystal. All of our diamonds come from legitimate sources in accordance with United Nations resolutions. Karine Chedid Joaillerie thus undertakes, according to the written guarantees issued by our suppliers, not to finance armed conflict. All our other stones come from suppliers labeled RJC (Responsible Jewelry Council), guaranteeing for our customers the origin of the stones ... As a gemologist, Karine carefully selects the center stones and makes a first pre-selection which will be presented during first dates.
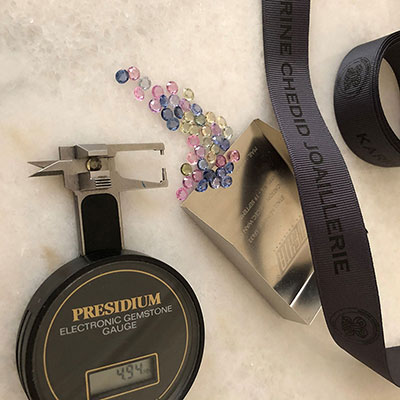
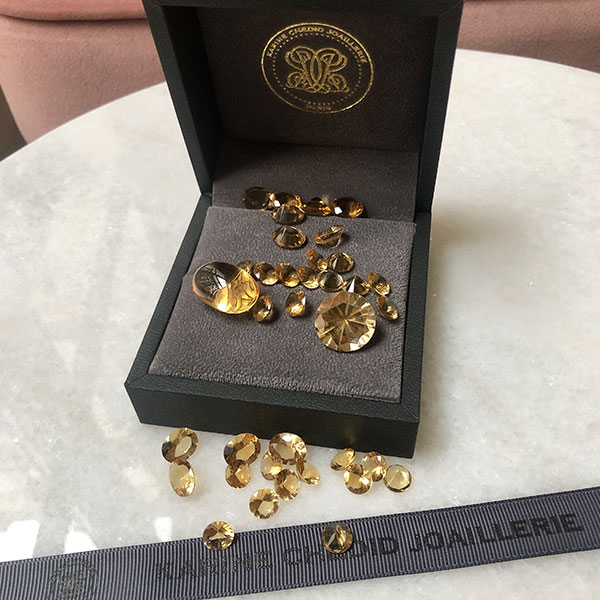
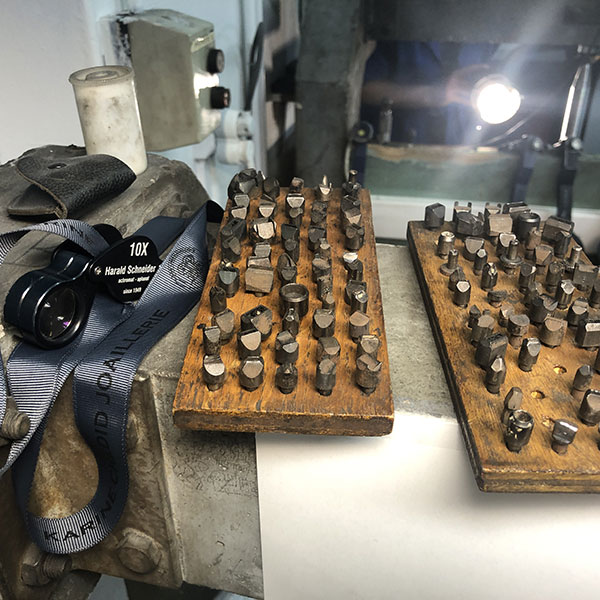
The lapidary
It is he who will have to re-cut a Family stone altered by daily wear for years. For example, emeralds have a hardness of 7.5 to 8 on the Mohs scale. They scratch more easily than sapphires or rubies which have a hardness of 9 on the same scale. The diamond presents the greatest hardness with a maximum score of 10. When an emerald is worn daily on an engagement ring, it is normal that its facets are damaged, it is said that it is chipped. For sapphires or rubies, even if they are less fragile, it is not uncommon to notice chipping or missing following impacts.In order to restore a Family stone to its beauty and shine of yesteryear, we can carry out a slight recutting, which will cause it to lose a little mass.
We may also need to re-cut a stone when you choose a vintage setting, in order to best fit it on the latter.
The 3D designer
The 3D designer
In the past, craftsmen sculpted wax ... Other times, other techniques: the 3D designer will transcribe the sketches of the jewel to be produced on his software. It is about modeling.He will then "print a wax", which will then be entrusted to the founder.

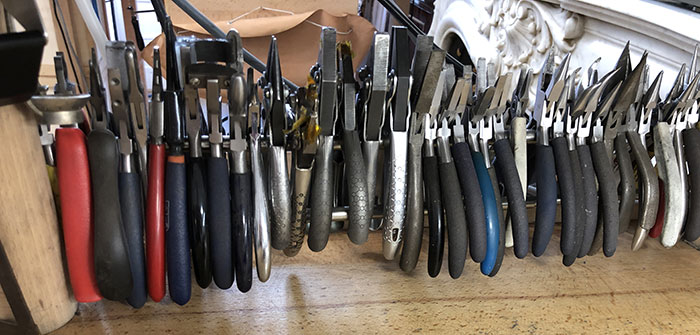
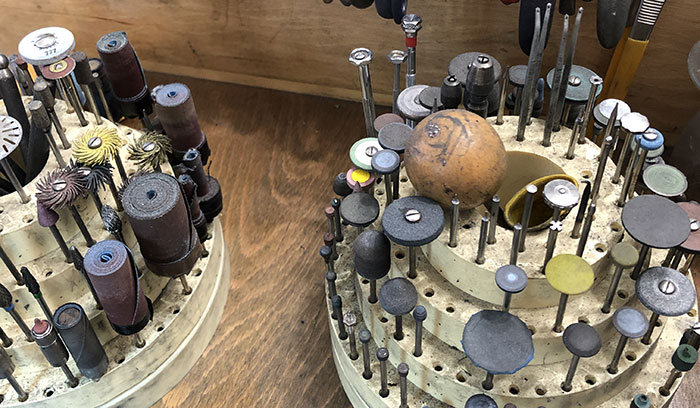
The Jeweler
Central pivot of the jewelry manufacturing cycle, it is he who will recover the "raw" cast iron and proceed to scraping, it is also he who will assemble the various elements designing the jewelry if necessary. He prepares the part for the crimper.Once recovered, it can continue to work on it, to give material effects with a satin or brushed finish for example.
For vintage jewelry that arrives at the workshop for refurbishment, it is he who will take stock of the condition of the part and who will suggest the necessary repairs, or even interesting improvements.
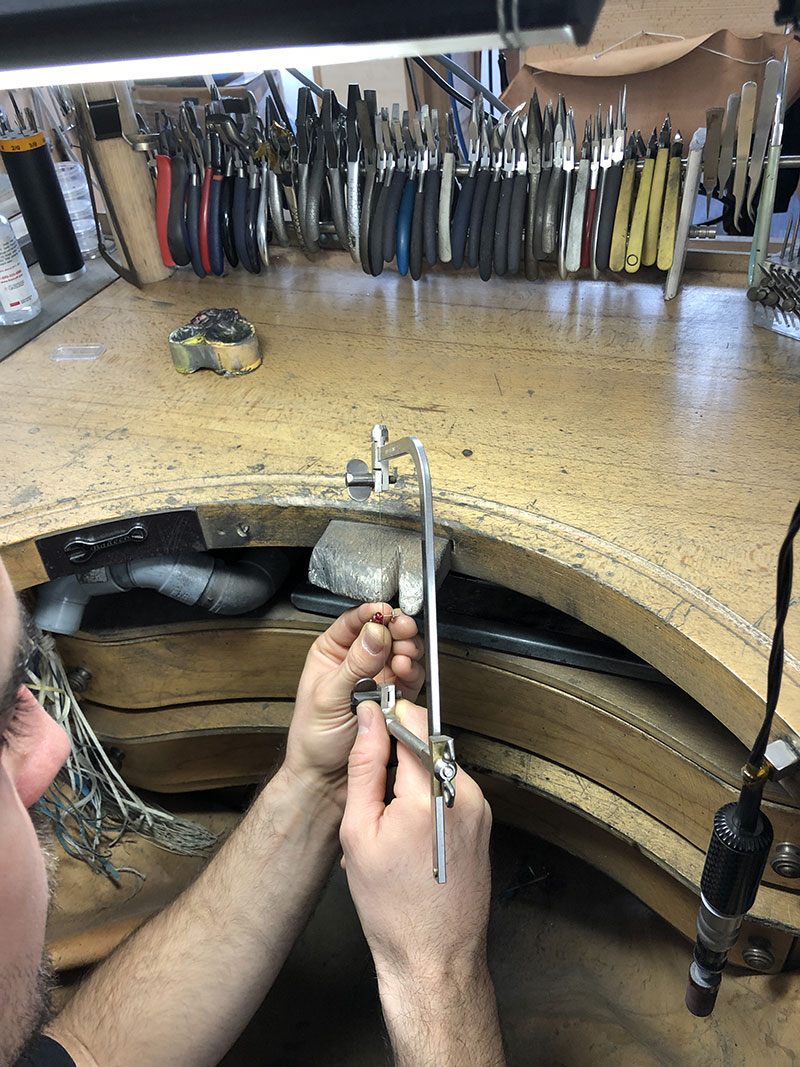
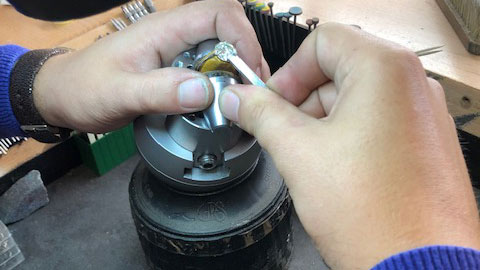
The crimper
He has the heavy responsibility of dressing the metal piece with carefully selected gems, thus giving life to the jewel.The apprenticeship is long and the best craftsmen are in great demand by the great Parisian jewelry houses. We have the chance to work with them and to offer this know-how to our customers.
The crimper has a whole series of possibilities including fillets, claws, scalloped, millegrains ...
The polisher
This is the final touch: the metal is polished to give it shine and sparkle. Often it is women who are found in these positions, no doubt because they are extremely meticulous ... On the other hand, you should not be too careful about your manicure when you exercise this profession because the dust of metal have the annoying tendency to become embedded in the smallest gaps, in particular under the nails ... We polish with the wheel or with the help of wires, in the old fashioned way.
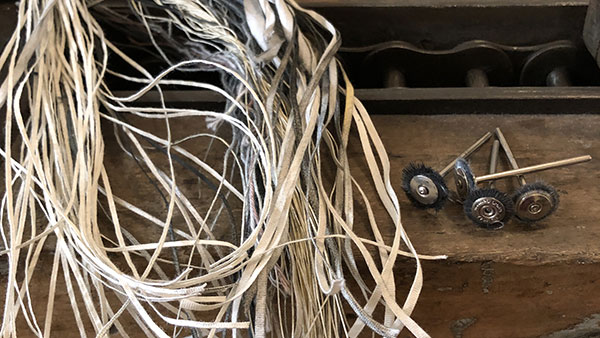